Oh dear! I’ve had some problems getting my nice shiny new railbus to work with a DCC decoder.
Getting access to the 21-pin socket in the roof of the model was not too difficult; it just needed determination, care and a couple pieces of plasicard. The problem arose when I plugged the decoder in. The engine would not run; it ran very smoothly using DC but there was no movement or sound when the decoder was fitted.
At first I thought that the decoder was faulty but quickly dismissed that theory when I fitted it into another loco and everything worked perfectly. I then tried fitting a known working 21-pin decoder in the railbus but still would not run. It didn’t make any sense to me as DC operation was OK with the blanking plate fitted. I contacted Tim at Arcadia Model Shop in Shaw where the loco had come from. He said that he didn’t know of any problems but offered replace it for me.
I had some further thoughts about the problem and came to the conclusion that the only explanation was that that the track pickups and motor drive connections had been reversed. The decoder is fitted to a 21-pin socket on a small PCB that has eight small sockets on it. Some of those sockets have fine plug-ended leads connected to them.
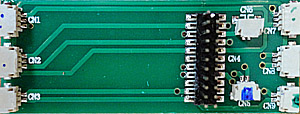
After some careful experimenting (the wires are very fine and only just reach the sockets in some cases) I found that the plugs in sockets CN5 and CN9 had been reversed. It was a bit if a stretch to get the plugs in the correct sockets as some of the wires had been kept as short as possible do to space constraints in the roof space but I managed to tease them out, refitted the PCB in the roof and installed the sound decoder again. Success! This time it all worked perfectly.
I have contacted Tim and let him know that I don’t need a replacement loco. I gave him the details of the factory assembly fault so that he can pass it back to Heljan. It does look as if they only test run the locos with the DC plate fitted and assume that all will be well when as DCC chip it fitted in it’s place.
The next job is to fit the speaker in a suitable position in the saloon where it won’t be too obtrusive. I think I’ll leave that for another day.